What Sets DTF Ink Apart from Other Printing Inks?
Unique ink properties
Start by understanding the differences between the inks on the market. Then we’ll see what makes DTF Ink different.
- Dye-based inks are often used to print photographs that come out with richer colors. However, it is prone to fading when exposed to sunlight.
- Solvent-based inks are renowned for their durability. weather-resistant and can often be seen being used for outdoor signage and banners.
- Eco-solvent ink is more environmentally friendly in its formulation, usually has little to no odor. It is commonly used for labels or packaging.
- Pigment ink is a type of ink that has smaller particle sizes, it also has good durability and is less prone to fading.
The DTF ink we are discussing today is actually some kind of ink between dye-based ink and eco-solvent ink.
You can think of it as pigment ink, but in current research, the formulation of pigment ink has been greatly improved, so it also has the advantages that eco-solvent ink has.
Powder is required post-printing
DTF ink is also unique in that it can be used in conjunction with DTF powder.
After printing a design onto a PET film, a layer of powder is applied to the surface, ensuring that can withstand washing much better after transfer.
Typically, DTF powder looks like this, and it gives the transferred image some durability.

Solving the problem of mass production of textile patterns
Not all types of fabrics are suitable for DTF printing, but it is an excellent method for printing designs onto garments such as T-shirts and POLO shirts that we often see.
Sublimation printing was originally widely used for fabric printing, but this method has difficult temperature control.
So direct-to-film (DTF) printing was developed to solve the problem of mass production on specific fabrics like pure cotton, which is commonly found in the market.
Key Components of DTF Ink and Their Roles
Pigment Concentration
High-quality DTF inks have a balanced pigment concentration that creates sharp, rich colors.
The key to this advantage is the ink’s constantly improving particle size.
This is also responsible for the smooth flow of the printhead, where the right balance of pigment loading and flow characteristics prevents clogging and ensures consistent output.
White ink for transfer
White ink is the most commonly used ink in DTF printing, and it needs to be fused with powder, then baked and melted to be transferred to the substrate.
Typically, DTF printing follows the logic of printing color before white.
How to Use DTF Ink for Optimal Results
Choosing the Right DTF Ink for Your Needs
Not all DTF inks are the same, and selecting the appropriate one depends on your specific printer and target fabric types.
It is essential to choose a DTF transfer ink compatible with your printer’s printhead technology. Incompatibility can lead to clogs, poor print quality, and even damage to the printer.
Proper Shaking and Preparation
In order to keep the ink in good pre-print condition at all times, all you need to do is to shake and stir the ink as much as possible before use to keep the particles in it from settling over time.
Shake it regularly even when it’s in storage. White ink, in particular, often needs to be “shaken” because of its frequent use in printing. There is also a device called “white ink shaking machine” on the market specifically designed to solve this problem.
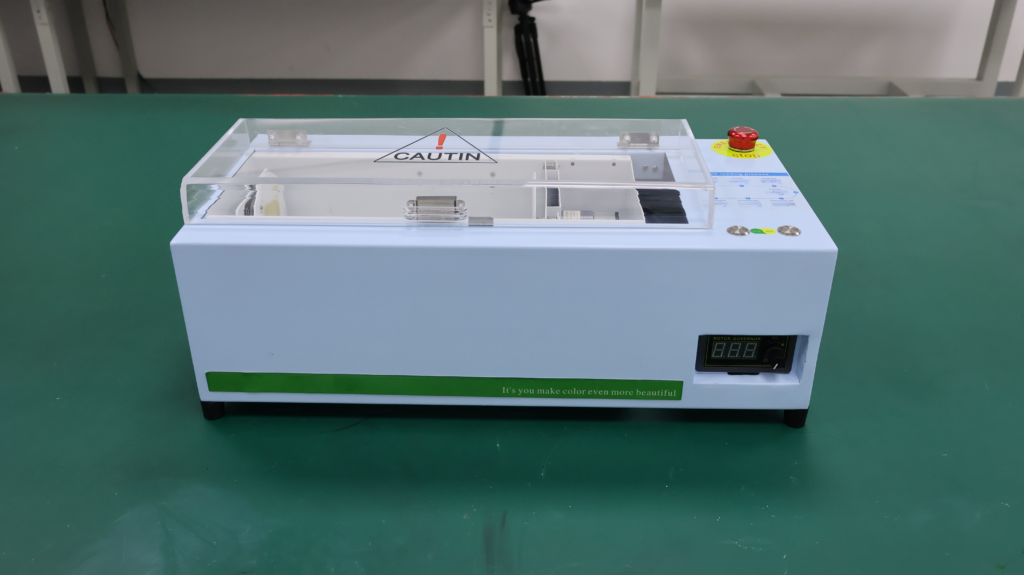
Correct Heat Press Settings
Using the correct heat press setting is critical to achieving a strong bond between the ink, powder and fabric.
Typically, heat press temperatures should be 145-165°C (293-329°F) for approximately 6-15 seconds, depending on fabric type.
Temperatures that are too low may result in inadequate bonding, while temperatures that are too high may damage the fabric or film.
A heat press is a piece of equipment that is often used when transferring films. There are different sizes of these machines. But as a rule, miniature heat presses are not used, as this affects efficiency.
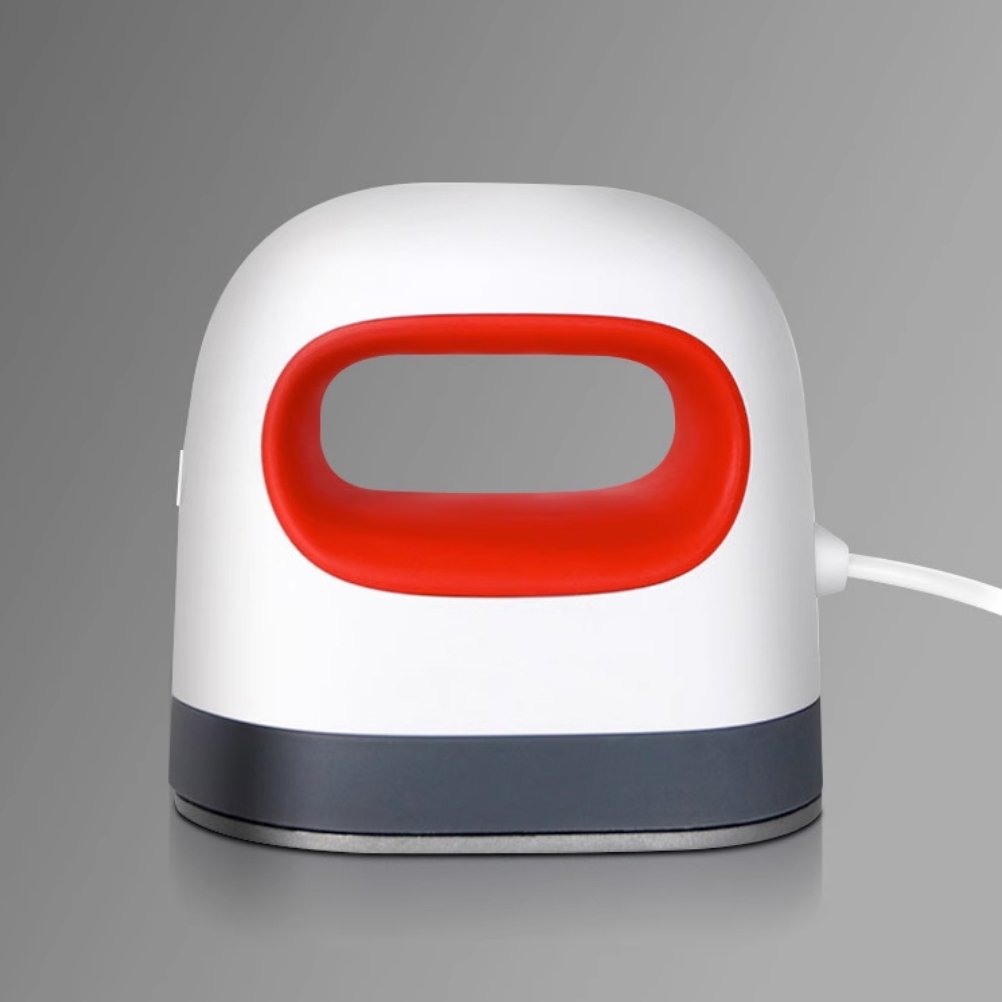


If you want to learn more about heat presses, you can click here.
Common Issues with DTF Ink and How to Avoid Them
Ink Clogging in Printheads
One of the more common problems when using ink is clogging, a problem usually caused by ink deposits or poor maintenance.
All you need to prevent clogging is to clean the printheads regularly and use compatible ink.
Faded Colors After Washing
Usually the finished product after DTF printing has a certain degree of cleaning resistance, as long as it is not repeatedly cleaned are within the scope of normal use.
There are many reasons for this, such as the quality of the ink or powder, or the temperature is not high enough during hot press transfer.
Room for Improvement in DTF Ink
Printing on a Wide Variety of Materials
What needs to be addressed at this stage is the specificity of DTF inks in terms of printing processes, such as the inability to print on a wider range of substrate types.
Once the ink is defined as only being able to print on a certain type of substrate, its innovativeness will be easily fixed, resulting in it not being able to appear in a wider market.
Avoiding waste in actual printing
Improvements at the formulation level allow the ink to be used more often. Which is also necessary considering all the waste that occurs in actual printing.
Summarize
DTF inks stand out for their unique blend of characteristics. Combining the durability of eco-solvent inks with the vibrant colors of pigmented inks.
It is ideally suited for printing on garments such as T-shirts and cotton fabrics. And is particularly well suited for mass production where heat-sublimation printing is ineffective.
While challenges such as printhead clogging and limited substrate compatibility remain, there is still room for improvement.