Why is there a lack of adhesion when using UV DTF inks?
The phenomenon that causes insufficient adhesion of UV ink is related to the following four factors:
Substrate surface problems
1.Substrate surfaces are too smooth: The surfaces of substrates such as glass, metal or some plastics are usually smooth, making it difficult for the ink to adhere. Especially in low temperature environments, these surfaces will appear “water mist”, resulting in the ink not being able to bond.
2.Substrate surface contamination: normal transfer before the need to clean up the substrate surface, do so in order to place the dust, oil or moisture residue, they will prevent the ink adhesion.
3.Low surface energy of the substrate: here the surface energy refers to the ink and the substrate before the bonding ability. Certain materials such as polypropylene (PP), polyethylene (PE), etc. have low surface energy and are not easy to combine with ink.
Ink Problems
1.Ink formulation mismatch: The ink is not optimized for the specific material or lacks adhesion enhancers. Different ink brands have different strengths, but differences in their formulations can lead to adhesion problems when adhering to the substrate.
2.Ink curing incomplete: UV light intensity or curing time is too short, resulting in ink is not fully cured and affect the adhesion. Previously we have explored the concept of UV light wavelength, ink curing and wavelength has a certain relationship. Wavelength mismatch usually affects curing.
Printing process problems
1.Insufficient inkjet volume for printing: Insufficient ink coverage will weaken adhesion. Insufficient coverage on the ink level will affect its adhesion, especially when printing more complex patterns.
2.Curing process temperature is too low: Some substrates require a higher temperature to activate the bonding properties with the ink. When the temperature required to fuse the substrate during transfer is not enough, the printed pattern will not be able to transfer up.
Environmental factors
1.High humidity: High humidity affects the initial adhesion of the ink. Temperatures in some areas are a nightmare for printing. Too high or too low a temperature can affect printing.
2.Unstable temperature: Low temperatures may retard ink curing and adhesion enhancement. High temperatures can accelerate ink curing and adhesion performance.
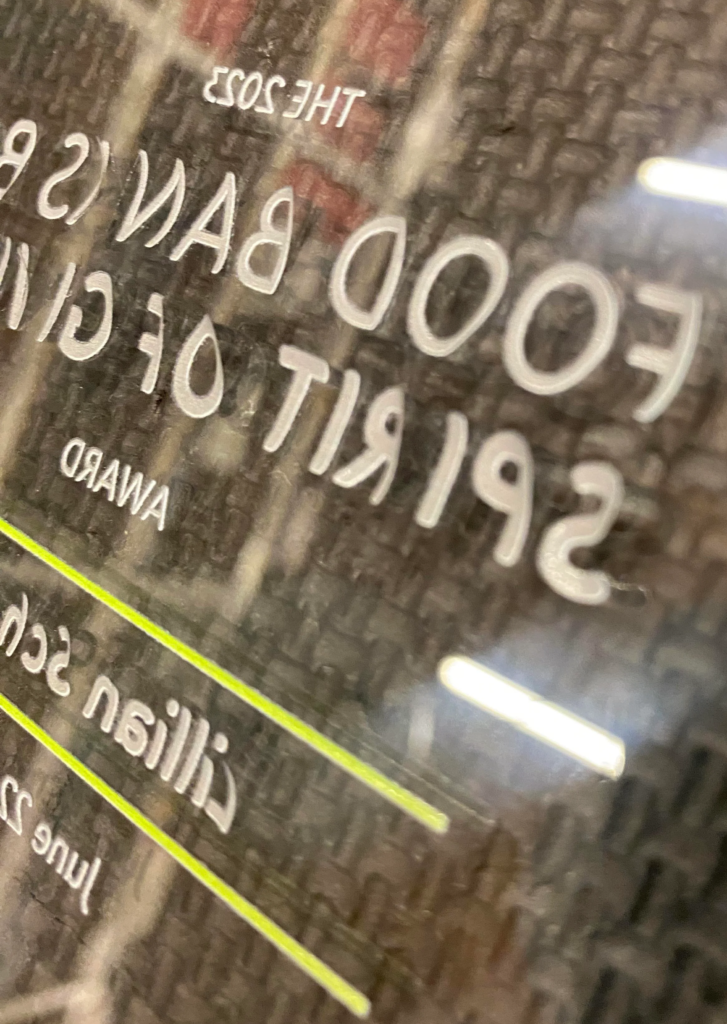
Solving the problem of insufficient adhesion when using UV DTF inks
After you understand the reasons why the ink does not have enough adhesion, you can determine the solution to the problem in some of these ways.
Optimizing material surfaces
Cleaning the surface: Use alcohol or special cleaners to remove oil, dirt and moisture from the surface.
Improve surface roughness: sand or sandblast smooth materials to increase ink adhesion points.
Surface treatment technology: For plastic or metal materials, corona treatment or plasma treatment can be used to enhance surface energy. For glass or ceramics, spray primer treatment can be applied to improve adhesion.
Adjust UV ink
Selection of suitable ink: Select special UV DTF ink (e.g. flexible ink, hard material ink) according to the printing material.
Add adhesion enhancer: Add appropriate amount of adhesion enhancer to the ink (need to confirm the compatibility with the ink brand or equipment manufacturer).
Optimize the printing process
Adjust the ink spray volume: Increase the ink spray volume appropriately to ensure that the pattern completely covers the target area.
Control curing conditions: Increase the intensity of the UV lamp to ensure that the ink is fully cured. Adjust the curing time and temperature according to the material properties (it is recommended to optimize the parameters through small sample testing).
Layered printing: For patterns with high adhesion requirements, better adhesion can be achieved by spraying and curing multiple thin layers.
Improved working environment
Control humidity: Control the working environment humidity within 40%-60% to reduce the interference of moisture in the air.
Stabilize temperature: Keep the printing and curing environment temperature at 20℃-25℃ to improve ink performance.
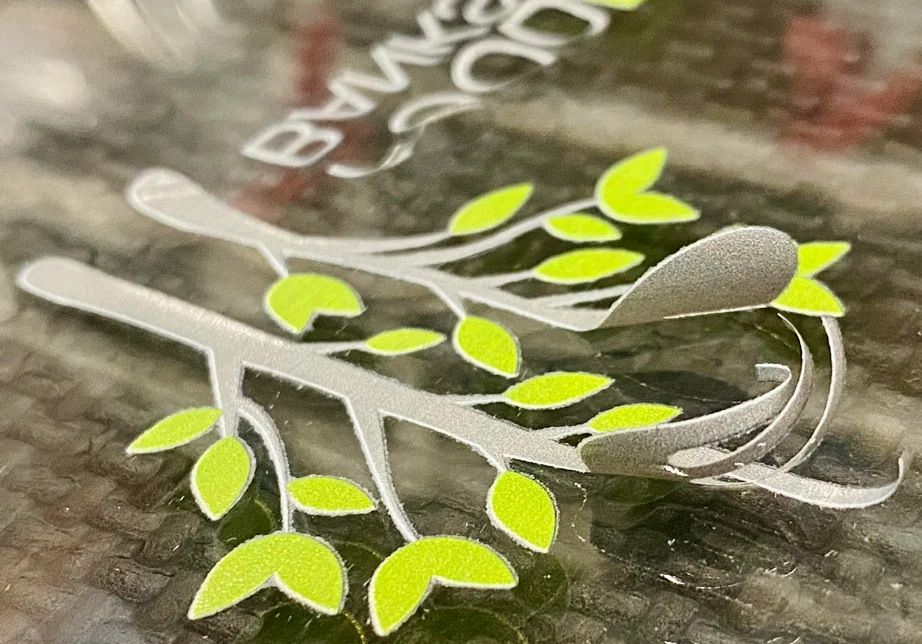
Tips for solving the lack of adhesion
Apply a layer of primer (Primer) that matches the UV ink before printing to enhance ink adhesion. Spray or brush the Primer evenly and wait for it to dry before printing. Common primers are suitable for glass, metal, plastic and other materials, and should be selected according to the specific material.
Adhesion Test
Hundred grid test method: use the blade to cut out the cross grid on the print pattern, and then use the tape to test the peeling situation to check the adhesion effect.
Adjustment and improvement: Optimize the process or consumables according to the test results.

Some method to prevent UV DTF inks from having insufficient adhesion
Selection of suitable materials: Select substrates with good UV ink compatibility at the design stage.
Regular maintenance of equipment: Ensure that UV lamps are of sufficient intensity and printheads are in good condition.
Standardize operating procedures: Record optimal printing and curing parameters to ensure consistent production.
Conclusion
The reasons for insufficient adhesion when using UV DTF ink are usually related to the material, ink, printing method, and environment. By troubleshooting the problem from each of these factors, you will be able to find a solution to the problem.