Analysis of the causes of UV DTF inks blistering problems
The following four factors can cause ink to bubble when printing, and you can determine the source of the problem based on these factors.
Ink quality problems
Ink formulation problems: Ink viscosity or surface tension (coverage/pressure) is not suitable for the substrate or film, and air bubbles are easily formed. If a similar situation occurs on the substrate, it is necessary to combine with the material of the substrate to make a judgment. If it is a similar problem on the film, through are related to the ink formula.
Air in the ink: Transportation or improper operation leads to air in the ink, forming tiny bubbles. Air and its dust are pervasive, so follow the User’s Guide for replacing ink and using ink.
Expired or improperly stored inks: Aging inks or improper storage conditions increase the risk of blistering during printing. Never use ink that has passed its shelf life! Also be sure to store it properly to avoid damaging the ink quality.
Printing equipment problems
Ink system problems: Air trapped in the ink tubes or printheads. In high-speed printers, the presence of air can cause ink and air to be output to the printing surface at the same time due to the flow force, which can lead to blistering.
Negative pressure control is not stable: the ink supply pressure is not stable, resulting in bubbles. Supply pressure can also be interpreted as the efficiency of the ink jet, sometimes fast and sometimes slow will lead to uneven ink jet, ink coverage sometimes big and sometimes small, resulting in bubbling in the gap.
Clogged or damaged printheads: Some of the nozzles do not work properly, making the ink jet uneven. A normally functioning printhead prints evenly, as long as you set up the printer. A portion of the nozzles not working leaves a gap between the ink and the ink.
Print process problems
Printing too fast: High speed printing can trigger an erratic flow of ink, which can create air bubbles. There are pros and cons to high-speed printing, and early on you may not be aware of the risks. Inevitably, the printer will cause bubbling after prolonged use!
Curing setting problem: UV lamp irradiation is too strong or at an inappropriate angle, resulting in instant curing of ink and blistering.
Material surface problems
Rough or porous substrate surface: If the substrate surface itself has fine bumps, then the ink cannot be evenly distributed and bubbles will easily appear. In this case either use a primer or replace the substrate.
Surface contamination: Oil or dust prevents the ink from adhering and bubbles may form. The presence of fine substances on the surface cannot be viewed with the naked eye, and they may be the cause of the bubbling!

Solving UV DTF Inks Blistering Solution
Optimizing UV DTF ink use
Air removal: Shake or stir the ink gently when using it to avoid air bubbles.
Choose high quality inks: High quality UV DTF inks are usually degassed and bubbles are less of a problem.
Ensure fresh ink: Replace ink regularly and avoid using expired or improperly stored ink.
Storage conditions: Store the ink in an airtight, constant temperature (18-25°C) environment, protected from light.
Check and maintain equipment
Clearing air from the ink path: Run an automatic or manual air venting program to ensure that there are no air bubbles in the ink tubes.
Adjust negative pressure: Check the printer’s negative pressure system to ensure a steady supply of ink.
Printhead Cleaning and Maintenance: Clean the printhead regularly to ensure that the nozzles are clear.
Ink circuit system sealing check: Confirm that there is no leakage of ink tubes and joints to prevent air from entering the ink circuit.
Adjusting Printing Parameters
Reduce print speed: Reduce the print speed appropriately to ensure smooth ink flow.
Optimize curing settings: Adjust the power and distance of the UV lamps to avoid excessive or fast curing. Select a step-by-step curing strategy (e.g. low intensity pre-cure + high intensity full cure).
Adjust inkjet volume: Increase or decrease the inkjet volume appropriately according to the material to avoid ink buildup or uneven distribution.
Prepare the material surface
Clean the surface: Clean the material surface with alcohol or dust-free cloth to remove oil and dust.
Surface treatment: Rough or porous surfaces can be coated (e.g. primer) to improve flatness. Corona or plasma treatment can be used on smooth surfaces to improve adhesion and reduce air bubbles.
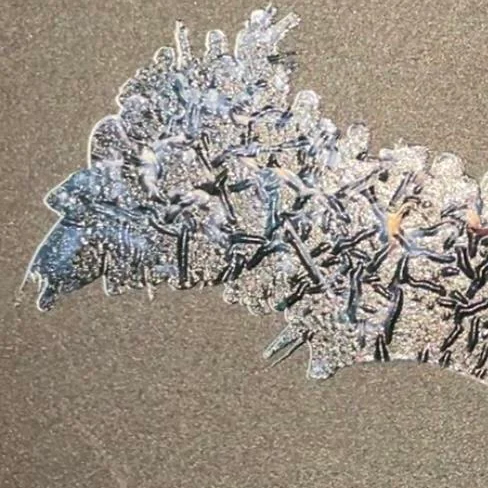
Further prevention of blistering of UV DTF inks
Stable production environment: Control the environment humidity at 40%-60% and keep the temperature at 20-25℃ to prevent the ink from blistering by the environment.
Regular equipment maintenance: Check the ink circuit, printhead and negative pressure system to ensure stable equipment operation.
Standardized operating procedures: Record the optimal printing, curing and surface treatment parameters to avoid bubbling problems caused by human operation.
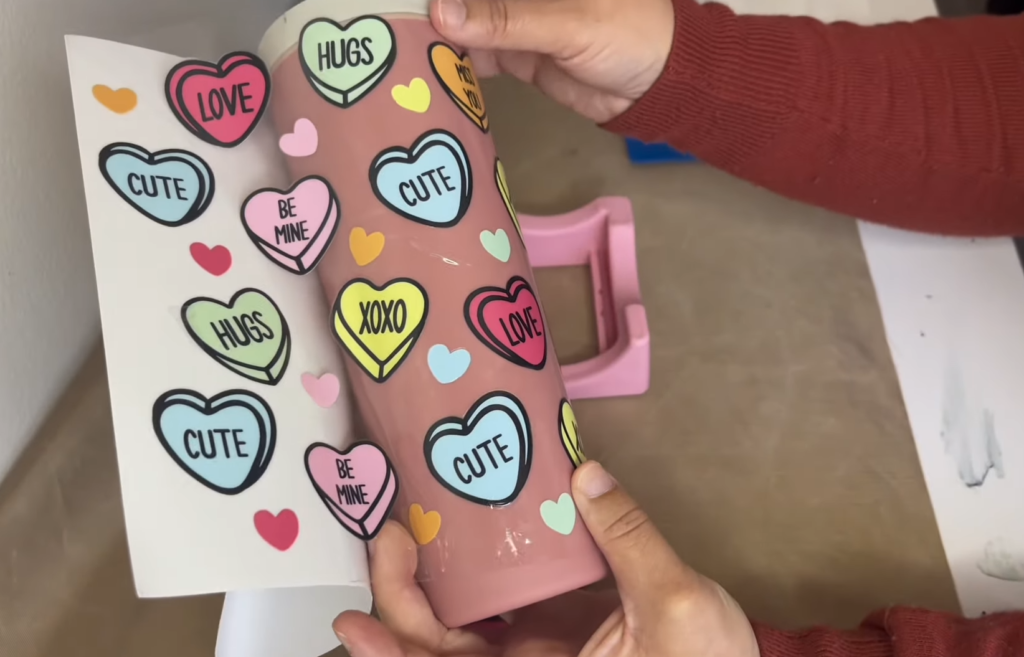
Conclusion
Blistering when printing with UV DTF inks is related to ink quality, printing equipment, printing process, and material surface. By checking each of these, you can identify the problem. After that, you only need to make adjustments in the specified manner to avoid similar phenomena.