Reasons Why DTF White Ink Cannot Be Covered
After the actual test, we get the conclusion that the cause is related to the ink, printing equipment, printing operations, substrates. The following will be analyzed one by one.
Ink problems
Insufficient covering power of white ink: Low pigment concentration of DTF white ink or uneven distribution of pigment particles leads to poor covering power. The amount of white ink used in printing is particularly large, and the coverage may be affected if it is not shaken well before use.
Ink formula incompatibility: poor adhesion or chemical compatibility between white ink and color ink. Different brands of ink have different production methods, and differences in raw material composition can lead to failure to cover.
Ink precipitation: Long time unused or insufficient mixing, the pigment in the DTF white ink is not evenly distributed. Pigment is the key to determine the color of ink, without pigment ink is like “cloudy water”.
Print device issues
Poor printhead condition: The DTF white ink printhead is clogged or aged and does not spray enough ink. A clogged printhead affects the ink jet, resulting in the proportion of ink used not going according to the rules set by the program.
Bubbles or clogged ink path: The presence of bubbles or impurities in the ink path leads to unstable white ink output. This is often a cause of clogged printheads as well.
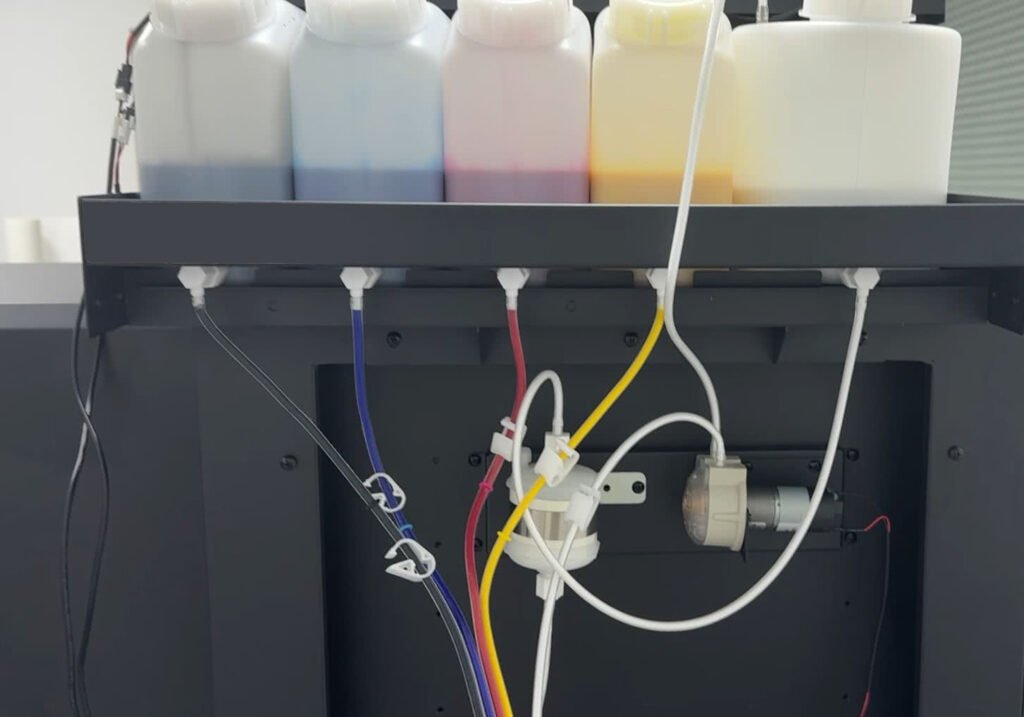
Printing process issues
White ink coverage is too thin: Insufficient DTF white ink jet to completely cover the color ink in a single print. Inadequate definition of ink usage on program settings leads to imbalance in design ratio.
Curing sequence problem: The color ink is not fully dried or cured, affecting the white ink adhesion effect. The time difference of curing will also cause the DTF white ink to reduce the coverage, should grasp the curing time to fully dry.
Insufficient resolution settings: lower print resolution, resulting in uneven white ink coverage. When the design of the image is more delicate, low print resolution will lead to uneven inkjet.
Substrate or material problems
Material unsuitability: Poor surface treatment of the substrate affects ink adhesion. Not all substrates are suitable for printing and need to be analyzed according to their surface conditions.

Color ink adsorption is too strong: the color ink penetrates or diffuses into the white ink layer, resulting in the DTF white ink can not be effectively covered. A similar phenomenon usually occurs when new and old inks are used interchangeably.
DTF White Ink Cannot Be Covered Solution
According to the cause analysis, we can find some solutions.
Optimized DTF white ink
Choose high-quality white ink: Choose white ink with high covering power and make sure its pigment concentration and particle distribution meet the requirements. As for what can be considered a high-quality white ink, it is recommended to follow the principle of “test before you buy”.
Stir the white ink regularly: White ink is prone to sedimentation, so it is recommended to stir it regularly to ensure that the pigments are evenly distributed. You can choose to buy a “white ink shaking machine” to solve the problem.

Check ink compatibility: Use white ink that is compatible with color ink to avoid adhesion problems caused by chemical incompatibility. Try to buy the same brand of white ink as the color ink.
Inspection and maintenance of equipment
Cleaning Printhead: Clean the white ink printhead regularly to prevent clogging or aging affecting the quality of ink jet. Usually the printheads for white ink and color ink are separate, so just pay attention to regular maintenance.
Exhaust and check the ink path: Use the exhaust function that comes with the printing device to remove air bubbles and impurities in the ink path to ensure a stable ink supply. Checking on your own is more detailed.
Calibrate printhead height: Adjust the height of the printhead according to the thickness of the material to ensure even coverage of white ink. The closer the printheads are to each other, the lower the strength of uniform ink coverage will be.
Adjust the printing process
Increase the amount of white ink jet: Adjust the ink output of the white ink channel appropriately to ensure the coverage effect. It can be tested before printing first. Also adjust according to the print design.
Layered printing: Use multiple printing (e.g. two white ink coverage) to improve the overall coverage. The coverage of single output white ink is not enough you can choose to output white ink twice.
Adjust the curing order: Make sure the color ink is fully cured before spraying white ink. Or spray white ink first for priming, then cover the color ink (depending on the process requirements). Increase the printing resolution: It is recommended to use 1440dpi or higher resolution to increase the fineness of white ink coverage.
Improved substrate treatment
Clean the surface of the substrate: Clean the substrate with alcohol or dust-free cloth to remove dust and oil. Avoid leaving impurities on the substrate to affect the coverage of white ink.
Use Primer: For high-gloss or low-surface-energy materials (e.g., metals, plastics), applying a primer can improve adhesion.
DTF Preventive Suggestions for Uncovered White Ink
Consistently taking precautions will minimize the occurrence of this phenomenon every time you do DTF printing.
- Regular equipment maintenance: Stir the white ink daily to prevent settling; clean the printheads and ink paths regularly to ensure smooth ink output. Especially if your print shop stores a large amount of ink, problems can easily arise if regular maintenance is not scheduled.
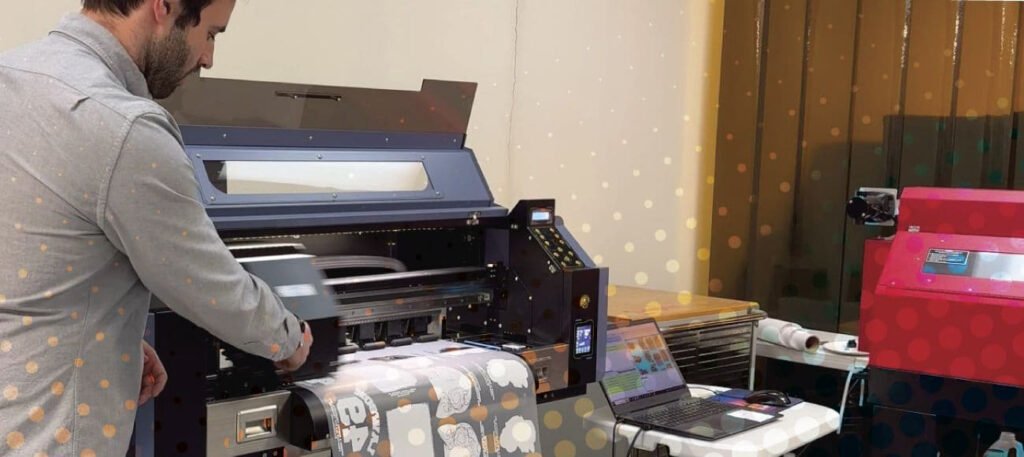
- Optimize print parameters: Save your best white ink coverage settings, including ink volume, curing time, and layering strategy. Thorough testing will save you from many headaches; don’t wait until the last minute.
- Test compatibility: Small sample tests are conducted before mass production to ensure good compatibility and coverage between white and color inks. Replacement of unused ink should also be tested to ensure consistent output.
- Choose quality consumables: Use the appropriate DTF ink and substrate to avoid white ink performance being affected by the quality of the consumables. Perhaps the cause of this phenomenon was not the ink in the first place.
Common Process Optimization Strategies
Ink coverage problems can also be solved by adjusting the print inkjet sequence. There are usually three options available:
Option 1: White before color
Printing order: spray a layer of white ink as a base layer first, and then spray color ink after curing.
Advantage: White ink acts as a masking layer and enhances the brightness and contrast of the pattern.
Option 2: Color first, then white
Printing order: Spray color ink first, then cover with white ink to enhance the back pattern coverage.
Advantage: Suitable for printing on transparent materials, white ink is used as a backlight masking layer.
Option 3: White color overlay
Multi-layer printing: spray white ink first, followed by color ink and white ink overlay in multiple passes to ensure uniformity and saturation.
Advantage: Suitable for products with high adhesion and high coverage requirements.
Conclusion
In short, when you encounter the problem that the ink can not be covered, you can analyze the above reasons, find the real reason, and then solve the problem through the corresponding solution. In addition, insist on good maintenance and prevention to avoid dropping the chain at critical moments.