What Does “Mix DTF Supplies” Actually Mean?
When we talk about “mixing DTF supplies,” we refer to the use of inks, powders, or films from different brands or incompatible formulations within the same printing process. Although they may appear similar on the surface, the chemical compositions of these materials often differ. For example, a user might run out of their usual white ink and substitute it with another brand’s product. At first, the print might seem normal. However, during heat pressing, unexpected results may occur: the ink may bleed, the colors might not cure properly, or the powder may fail to adhere evenly. These seemingly small substitutions can snowball into major production issues.

Common Examples of Mixing
Most often, many people will choose to use up a batch of supplies and then choose to buy a different brand of a particular type of supplies separately. For example, I have quite a bit of DTF film and DTF powder left, but I ran out of ink. As a result, I choose to purchase cheaper or more expensive inks to ensure that my current output will meet expectations.
While each consumable may work well on its own, their interactions can be unpredictable. For example, the ink may also fail to bond to the film coating, resulting in blurred outlines or ink buildup.
Why Users Mix Materials: Cost, Convenience, Misunderstanding
There are several reasons why users mix consumables:
- Cost: Trying to cut down on expenses by buying cheap supplies, thinking compatibility will solve most problems.
- Convenience: A quick solution to the problem of replenishment of consumables, especially when it comes to high-volume production inputs, but not enough consumables in stock.
- Misconception: Many users believe that all DTF materials are compatible with each other and that their production processes are the same. Slight differences in composition can seriously affect the results.
The Risks of Mix DTF Supplies
Mixing DTF supplies introduces multiple points of failure during printing. These issues are often subtle at first but can lead to irreversible equipment damage and production inconsistencies.
Chemical Incompatibility Can Clog Printheads
Frequent ink changes are a relatively common occurrence. This time people always forget to clean the printer before changing the ink. This leads to mixing between different brands of ink.
When inks from different brands are combined, their chemical stabilizers may conflict. For example, a pigment suspension in one ink may react with the surfactant in another, leading to coagulation. This coagulated mixture gets stuck in the printhead nozzles, blocking ink flow. The result? Broken lines, sputtering, and eventually, a non-functional printhead.
Poor Color Output and Print Inconsistencies
Color accuracy in DTF printing depends heavily on the precise interaction between ink, film coating, and powder. When these components are mismatched, the color gamut shifts. Prints may appear faded, washed out, or show uneven saturation. You might see banding, unexpected undertones, or ghosting effects across what should be solid-colored areas.
Film and Fabric Adhesion Problems
A mismatch between powder and film often results in poor transfer quality. For example, if the powder doesn’t melt uniformly due to chemical mismatch, it won’t bond with the fabric correctly. This leads to issues like peeling edges, cracking after a few washes, or transfers that feel rough and uneven. These problems damage customer trust and brand reputation.

Long-Term Effects of Mix DTF Supplies on Printers and Workflows
Even if short-term prints look acceptable, long-term use of mixed supplies increases maintenance demands and shortens printer lifespan.
Higher Cleaning and Maintenance Frequency
Residues from incompatible materials tend to build up in the capping station, ink tubes, and dampers. As a result, cleaning cycles become more frequent and intensive. In extreme cases, users must perform manual cleaning or even disassemble parts of the printer to remove hardened ink residue.
Accelerated Wear on Printer Components
Inconsistent ink viscosity can place additional pressure on pumps and printhead valves. Over time, the irregular flow rate causes mechanical strain, resulting in premature wear and a higher risk of hardware failure. Repairs can be costly and time-consuming.
Unexpected Downtime and Workflow Disruption
When something goes wrong due to mixed materials, it’s rarely easy to fix. Troubleshooting becomes more difficult because you’re working outside the intended system specifications. Production delays often follow, with missed delivery deadlines and unhappy customers.
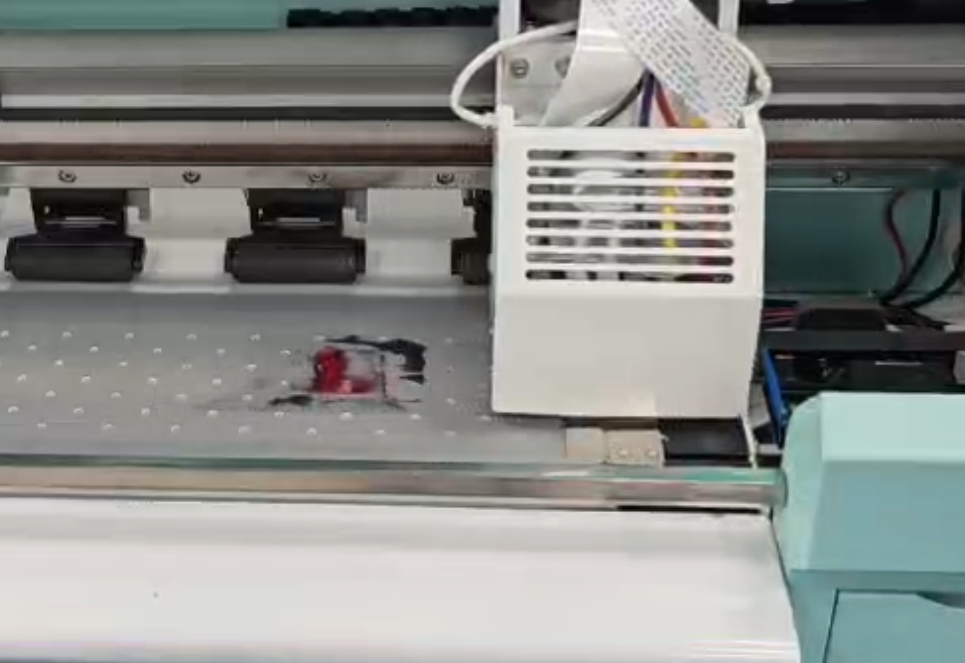
Additional Costs Incurred By Mix DTF Supplies
Beyond technical headaches, mixing supplies leads to waste, inefficiency, and higher overall costs.
Material Waste and Reprint Costs
Misprints, peeling transfers, or incorrect colors mean the entire job must be redone. This not only wastes ink and film but also increases power consumption and operator time. In high-volume settings, these costs compound quickly.
Loss of Efficiency and Time
Operators waste time adjusting settings, cleaning clogs, or figuring out why colors are off. All of this takes away from productive printing time, reducing your overall output.
Risks of Voiding Manufacturer Warranty
Most printer manufacturers and suppliers specify which inks and materials are approved. Using third-party consumables not listed in their guidelines can void your warranty, leaving you on your own when hardware issues arise.
How to Avoid the Pitfalls of Mix DTF Consumables
Fortunately, the risks associated with mixed supplies are avoidable. The key is consistency and awareness.
Stick to The Same Brand Of Ink, Film and Powder Sets
Manufacturers test their materials for compatibility. Using the full set from the same brand ensures cohesive chemical interaction and stable printing output. It’s not just a marketing pitch — it’s a technical necessity.
Opt for Suppliers Offering Complete, Compatible Systems
Choose suppliers that offer complete DTF kits or compatible systems, including DTF ink, film, and hot melt powder. This reduces guesswork and saves time on quality testing. Ask if they have conducted adhesion tests and compatibility trials on their product portfolio.
We offer a whole range of products relating to DTF printer supplies, click here to view them.
Test Before Scaling to Production
If you do need to try a new material, always run controlled print tests first. Evaluate color, adhesion, and wash resistance before using it in large-volume orders.


Conclusion
Mixing DTF supplies might seem harmless, even cost-saving at first. But as we’ve seen, the technical, financial, and operational risks far outweigh any short-term convenience. In DTF printing, consistency isn’t just good practice — it’s essential for protecting your equipment, your workflow.