Why Does DTF Pigment Ink Color Deviation Occur
DTF printing ink quality issues
Ink is the most consumed consumable in the printing industry. That’s why most printers purchase large quantities of ink from a trusted ink supplier for back-up purposes.
Long-term partnerships don’t guarantee the complete absence of occasional batches of substandard ink. You can try printing a test strip to make sure that there is no problem with the ink.
Printing settings issue
Printing jobs often involve switching between simple and complex designs. This frequently leads to inconsistencies in settings, resulting in color variations due to incorrect print configurations.
if your printing needs are more precise.
Low white ink layer coverage
White ink underprinting is necessary in DTF printing to provide a base for other colored inks. The purpose is to enhance the brightness of the other colors. Consequently, if the red ink is not adequately primed with white ink at the time of printing, then it is at risk of color deviations in subsequent processes.
See also: why does the DTF white ink not cover the color ink?

Baking error
After the ink is printed onto the film, the film is dusted with powder for subsequent baking. If the baking setting is incorrect, it may also cause color deviations in the ink.
The printer is broken
If you have checked all these problems and found no problems, then this is the time to see if there is a problem with the printer. The factors that may cause the printer to deviate from the ink color are usually in the print head and the ink loading system. You need to check these areas for problems.
How To Solve DTF Pigment Ink Color Deviation
Check and replace DTF printing ink
Selection of high-quality ink: Ensure that the ink is from a reliable source, has pure color and is optimized for the DTF process.
Stir well: Ink that has not been used for a long time may settle, shake or stir well before use to restore color performance.
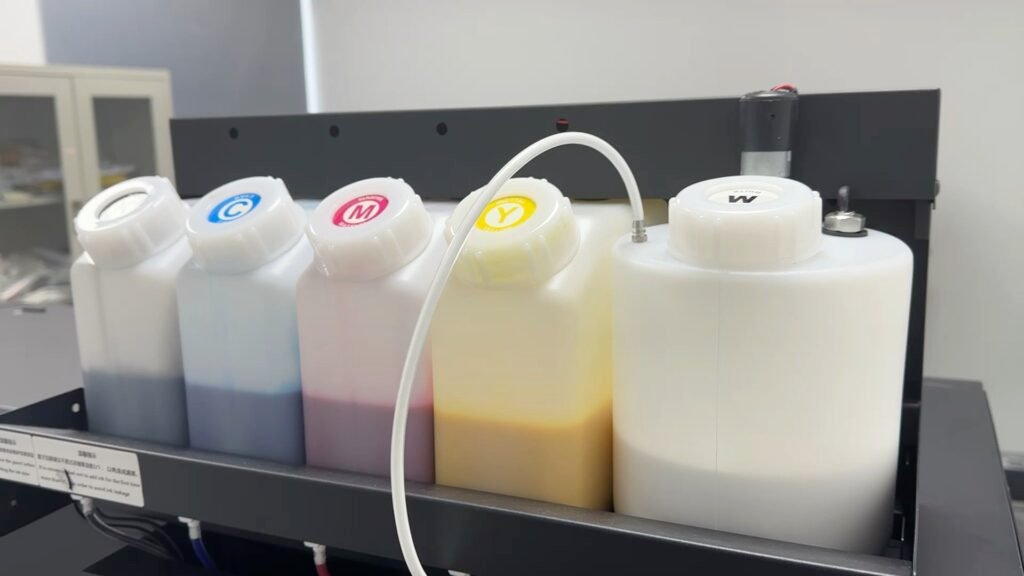
Optimize print settings
Adjust the ICC profile: Create an exclusive ICC file through the color calibration equipment to ensure accurate color output.
Increase the amount of red ink jet: Appropriately increase the ink concentration or print intensity of the red channel to enhance saturation.
Increase resolution: Choose a higher print resolution (e.g. 1440 dpi) to enhance color expression.
Checking the white ink layer
Improve white ink coverage: Ensure that red areas are primed with enough white ink to enhance the brightness and purity of the red color.
Check the printing order of white and color inks: Ensure the white ink is fully dry before applying the red ink.
Optimization of baking and transfer processes
Control temperature and time: Avoid too high baking or transfer temperature, it is recommended to test the best conditions in the range of 160℃-180℃.
Uniform application of hot melt powder: Ensure that the hot melt powder is uniformly applied without affecting the color performance.
Inspection equipment
Cleaning the printheads: Clean and maintain the printheads regularly, especially the red channel, to prevent clogging or color mixing.
Check the DTF printing ink path: Clean the ink path of possible impurities or residual yellow ink to ensure pure red ink output.

Replacement or optimization of film materials
Test different brands or types of DTF films to select a coating with better ink compatibility and improved color reproduction.
Some Prevention Tips For DTF Pigment Ink
Choose high-quality consumables
High-quality DTF pigment inks, hot-melt powders and film materials can reduce color deviation problems.
Regular equipment maintenance
Keeping printheads and ink paths clean reduces color problems caused by equipment.
Optimize process parameters
Record the best printing, baking and transfer parameters to form a stable production standard.
Control environmental conditions
Maintain appropriate temperature and humidity (40%-60% humidity) to avoid environmental impact on ink and film materials.
Conclusion
Achieving accurate red ink output in DTF printing requires careful attention to several factors including the quality of the ink, proper print settings, sufficient white ink coverage, precise baking conditions, and well-maintained printing equipment.
Consequently, addressing these elements by using high-quality consumables, adjusting ICC profiles, and ensuring optimal process parameters can significantly mitigate the color deviation issue and lead to more consistent and vibrant printing results.
These situations are the answers about the deviation of DTF ink color. When you encounter these phenomena, you can first find out their causes and then go for problem solving. You can ask the supplier from whom you purchased the printer.